How Rotational Molding is Revolutionizing Plastic Production
How Rotational Molding is Revolutionizing Plastic Manufacturing
Rotational molding, usually named rotomolding, has emerged as a innovative technique in the world of plastic production. Having its ability to produce tough, light, and easy services and products, this production process is fast increasing traction across industries including automotive to customer goods. But why is Plastics Rotomolding so special? Let's discover how this revolutionary method is reshaping how plastic items are designed, created, and used.
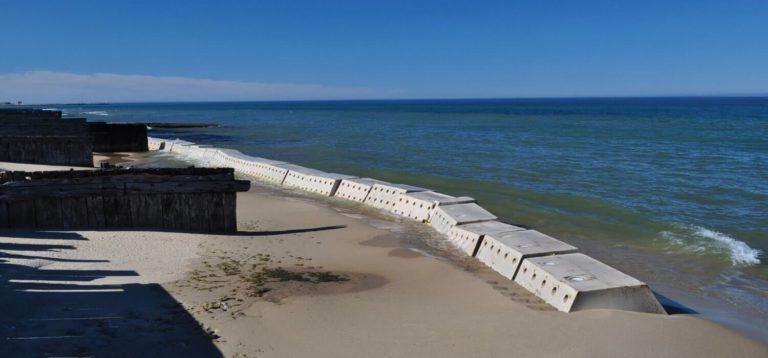
What's Rotational Molding?
Rotational molding is a production process that employs temperature and rotation to produce hollow plastic objects. Unlike treatment or blow molding, this approach doesn't rely on high pressure. As an alternative, it requires placing plastic dust or resin in the mold, that will be then heated and rotated on numerous axes. The product sticks to the mold's inner floor, growing evenly spread walls. After the shape cools, the completed solution is removed, prepared for use.
Important products and services produced through rotational molding include storage tanks, outdoor furniture, games, and also medical equipment. Its versatility and effectiveness make it a sought-after method across diverse sectors.
Benefits Driving the Popularity of Rotational Molding
1. Design Mobility
Rotational molding permits the development of delicate, complex shapes without compromising structural integrity. That flexibility provides makers the capability to produce custom designs while preventing costly tooling expenses. Services and products can contain integral functions like threads, positions, and multiple chambers, lowering the requirement for construction and extra parts.
2. Cost-Effectiveness
Compared to high-pressure techniques like procedure molding, rotational molding boasts lower tooling costs. Furthermore, this technique is less energy-intensive, which makes it not only cost-effective but in addition environmentally friendly. Its capacity to create durable components with little spend also adds to their appeal.
3. Standard Thickness and Toughness
Rotational molding guarantees a straight circulation of material throughout the mold's surface, ultimately causing standard wall thickness. The end result? Products which are structurally powerful, resilient to stress, and long-lasting. That makes it a perfect choice for goods exposed to tough environments, such as water tanks and professional containers.
4. Product Usefulness
The procedure accommodates a wide selection of materials, including polyethylene, polypropylene, and plastic, catering to different business requirements. These products may also be UV-stabilized or flame-retardant for particular applications.
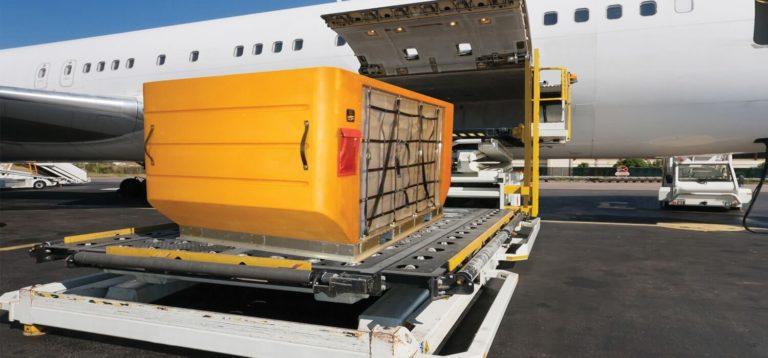
Surrounding the Potential of Plastic Manufacturing
Rotational molding's benefits ensure it is a standout method in the growing landscape of plastic manufacturing. Their capability to merge cost-efficiency with modern design and longevity is a testament to their affect industries worldwide. With developments in products and technology, rotational molding may truly continue steadily to revolutionize how plastic items are manufactured, meeting the rising needs for quality, sustainability, and creativity.